По данным Массачусетского технологического института, инженеры продемонстрировали первый полностью напечатанный на 3D-принтере двигатель с выпускающим капли электрораспылением. Их устройство, которое можно изготовить быстро и за небольшую часть стоимости традиционных двигателей, использует коммерчески доступные материалы и методы 3D-печати. Устройства можно даже полностью изготовить на орбите, поскольку 3D-печать совместима с производством в космосе.
Двигатель с электрораспылением применяет электрическое поле к проводящей жидкости, образуя высокоскоростную струю крошечных капелек, которые могут двигать космический корабль. Эти миниатюрные двигатели идеально подходят для небольших спутников под названием CubeSats, часто используемых в академических исследованиях.
Поскольку электрораспылительные двигатели используют топливо эффективнее мощных химических ракет, используемых на стартовой площадке, они лучше подходят для точных маневров на орбите. Тяга, создаваемая электрораспылительным излучателем, невелика, поэтому в электрораспылительных двигателях обычно используется ряд излучателей, равномерно работающих параллельно.
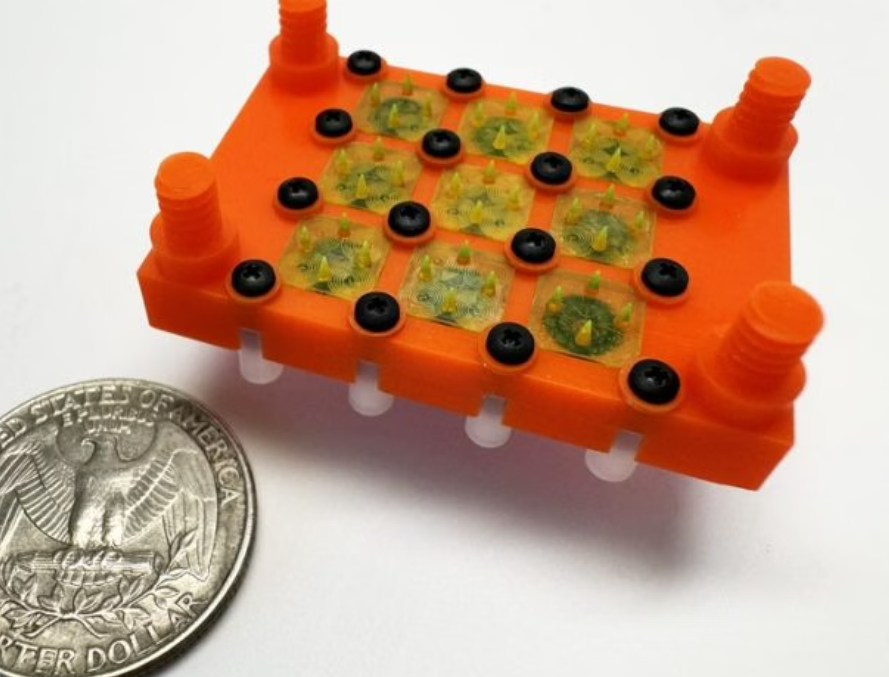
Однако эти мультиплексные двигатели с электрораспылением обычно изготавливаются с помощью дорогостоящего и трудоемкого производства полупроводников в чистых помещениях, что ограничивает, кто может их производить и как можно применять устройства.
Разработав модульный процесс, объединяющий два метода 3D-печати, исследователи Массачусетского технологического института преодолели трудности, связанные с изготовлением сложного устройства, состоящего из макро- и микроразмерных компонентов, которые должны безупречно работать вместе.
Их проверенный концептуальный двигатель состоит из 32 электрораспылителей, работающих вместе, создавая стабильный и равномерный поток топлива. Трехмерное печатное устройство генерировало такую же или даже большую тягу, чем существующие электрораспылительные двигатели, выпускающие капли. Посредством этой технологии астронавты могут быстро напечатать двигатель для спутника, не дожидаясь, пока его отправят с Земли.
«Использование производства полупроводников не совпадает с идеей недорогого доступа в космос. Мы хотим демократизировать космическое оборудование. В этой работе мы предлагаем способ создания высокопроизводительного аппаратного обеспечения с технологиями производства, доступными для большего количества игроков», – сказал Луис Фернандо Веласкес-Гарсия, главный научный сотрудник Microsystems Technology Laboratories (MTL) Массачусетского технологического института.
Двигатель с электрораспылителем имеет резервуар топлива, протекающий через микрофлюидные каналы в серию излучателей. На кончике каждого эмиттера действует электростатическое поле, вызывающее электрогидродинамический эффект, формирующий свободную поверхность жидкости в конусообразный мениск, выбрасывающий поток высокоскоростных заряженных капель со своей вершины и создающий тягу.
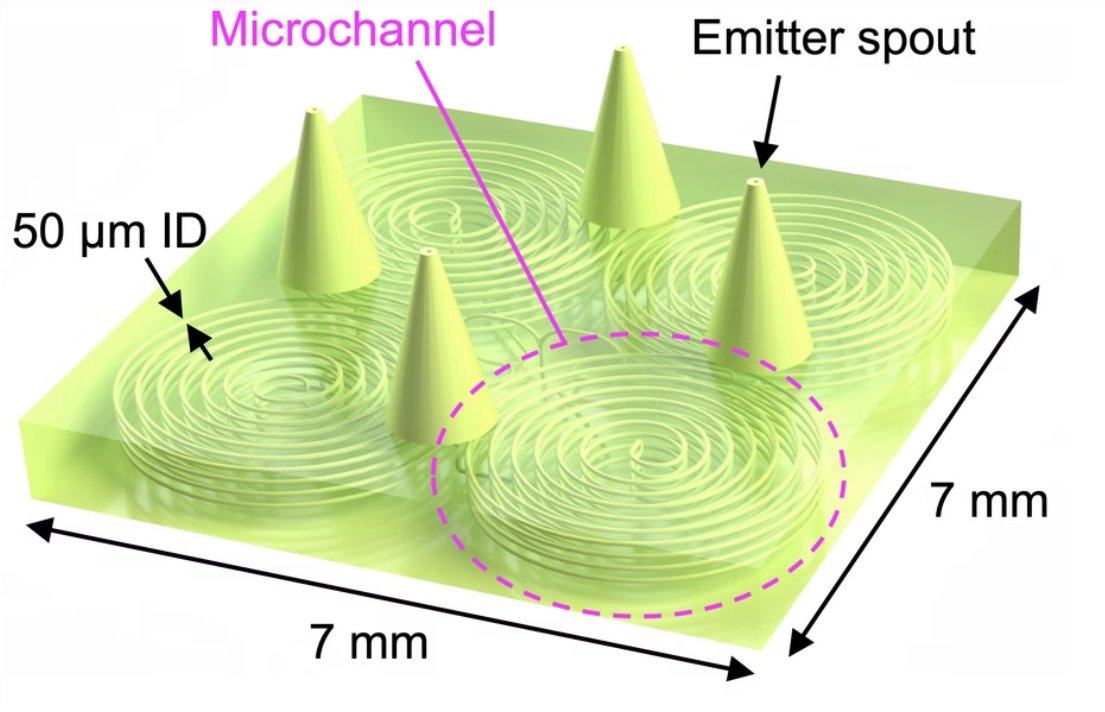
Наконечники эмиттера должны быть как можно более острыми, чтобы достигнуть электрогидродинамического выброса топлива при низком напряжении. Устройству также необходима сложная гидравлическая система для хранения и регулирования потока жидкости – эффективного перемещения топлива через микрофлюидные каналы.
Эмитерный массив состоит из восьми эмиттерных модулей. Каждый модуль излучателя содержит массив из четырех отдельных излучателей, которые должны работать в унисоне, образуя большую систему взаимосвязанных модулей.
«Использование универсального подхода к изготовлению не работает, поскольку эти подсистемы имеют разные масштабы. Наше главное понимание заключалось в том, чтобы объединить аддитивные методы производства для достижения желаемых результатов, а затем придумать способ объединить все, чтобы детали работали вместе как можно эффективнее», - сказал Веласкес-Гарсия.
Чтобы достичь этого, исследователи использовали два разных типа фотополимеризационной печати в кубе (VPP). Исследователи изготовили модули излучателя с помощью двухфотонной печати (2PP). В этой технике используется высокосфокусированный лазерный луч для затвердения смолы в точно определенной зоне – создание трехмерной структуры по одному крохотному кирпичику или вокселю за раз. Этот уровень детализации позволил им создавать очень острые наконечники излучателей и узенькие однородные капилляры для транспортировки горючего.
Модули излучателей помещены в прямоугольный корпус, называемый коллекторным блоком, который удерживает каждый на месте и снабжает излучатели топливным топливом. Коллекторный блок также интегрирует модули эмиттера с электродом-извлекателем, запускающим выброс топлива из наконечников эмиттера. Изготовление большего коллекторного блока с помощью двухфотонной печати было бы невозможно из-за низкой пропускной способности метода и ограниченного объема печати.
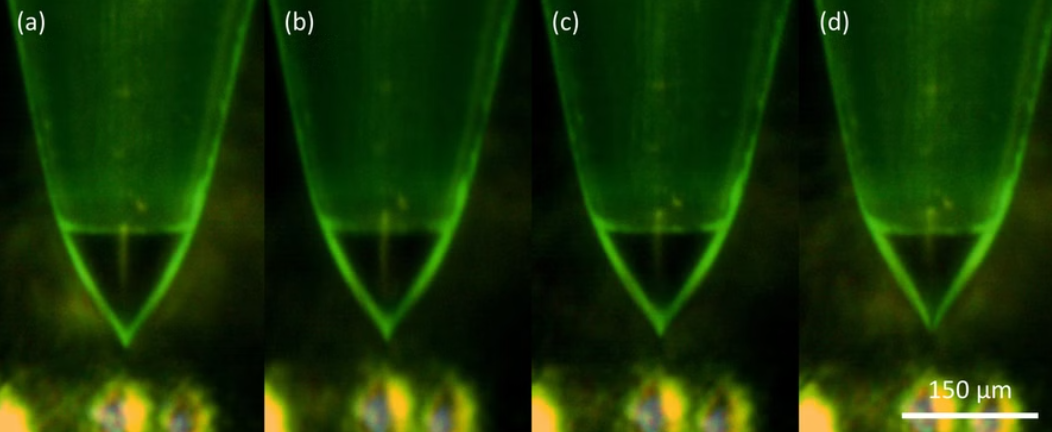
Вместо этого исследователи использовали цифровую обработку света (DLP), которая использует проектор размером с чип, чтобы осветить смолу, утверждая один слой 3D-структуры за раз.
Однако 3D-печать компонентов электрораспылительного двигателя — это лишь половина успеха. Исследователи Массачусетского технологического института также провели химические эксперименты, чтобы убедиться, что печатные материалы совместимы с электропроводным жидким топливом. В противном случае топливо может разъесть двигатель или вызвать его трещины, нежелательные для аппаратного обеспечения, предназначенного для длительной работы без технического обслуживания.
Они также разработали метод скрепления отдельных частей между собой таким образом, чтобы избежать смещений, которые могут ухудшить производительность и обеспечить водонепроницаемость устройства. В конце концов, их 3D-печатный прототип смог генерировать тягу более эффективно, и превзошел существующие капельные двигатели с электрораспылением.